Plate and gasket (and tube style) heat exchangers function effectively due to their incredible exposed surface area. During routine inspection, a technician breaks the unit down to inspect sanitary contact surfaces. The technician applies dye to one side of the clean tubular or plate surface before visually inspecting for bleed-through.
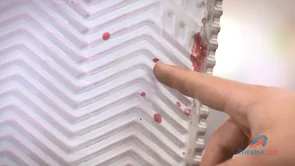
This method is time-tested, but costly, and subject to human error. Partial or total disassembly is required to perform a dye test. The technician is responsible for finding 100% of holes while inspecting up to thousands of square feet of surface. Downtime and costs can rise unexpectedly while the technician searches for a needle in a haystack. A contaminated process is still possible afterward. What other options exist?
Thermaline CCT 4.0 - Testing, Automated
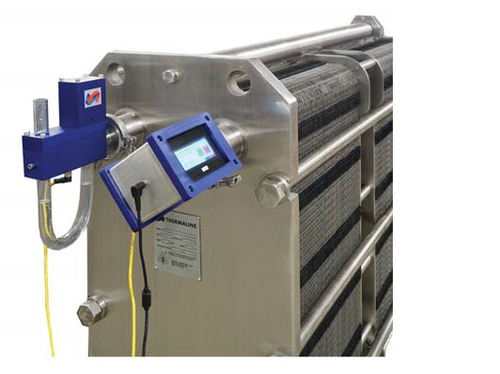
Thermaline's patented Cross Contamination Tester 4.0 has been introduced as the new standard for primary testing of tubular and plate and gasket heat exchangers. The unit remains completely assembled while the automated tester is installed and operating. Cross contamination detection and data are recorded on the spot. If any leaks between process and media are detected, installation of a fresh Thermaline plate and gasket pack can begin at a scheduled time. Unlike the traditional breakdown, cleaning, and dye testing process, there is no chance for human error!